Four Demands That Industry 4.0 Places On CNC Machine Controllers
Industry 4.0 is reshaping manufacturing in the same way that Amazon transformed retailing. By embracing the best practices, CNC machine builders can create new product offers and can identify opportunities to plug into smarter factories capable of automatically taking corrective or optimizing actions. Understand the one key machine automation architecture element that will determine success or failure.
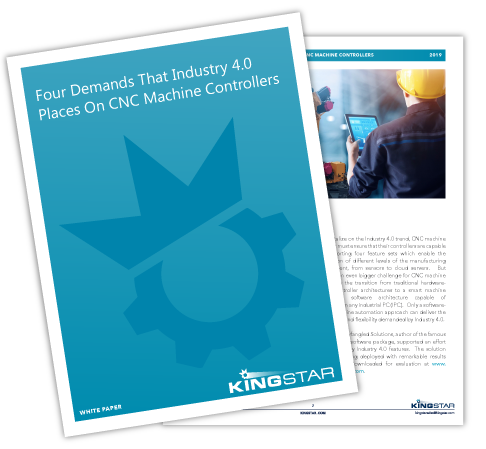
- Defines the role machine automation plays in Industry 4.0
- Explores the key feature sets required by CNC machine controllers
- Identifies key standards that are emerging and important
- Explains why 1 fieldbus stands apart in supporting IIoT
- Reveals the 1 architectural element that is the perquisite for success
Please fill out the form below to access the report.
In this white paper, “5 Real-Time, Ethernet-Based Fieldbuses Compared,” we examine five different protocols that claim to offer the best price/performance open standard for real-time Ethernet fieldbuses. Topics covered include:
5 standards compared: Ethernet/IP, Ethernet Powerlink, EtherCAT, PROFINET IRT, & SERCOS III
Evaluation of standards bodies, philosophies, and architectural underpinnings, response time, jitter, data rate, and more
Fieldbus scorecard: which standard wins in price/performance and market acceptance?
Understand your options when it comes to real-time, Ethernet-based fieldbuses. Read the white paper to see how the top five standards stack up.