Hierarchy of Industrial Automation Systems
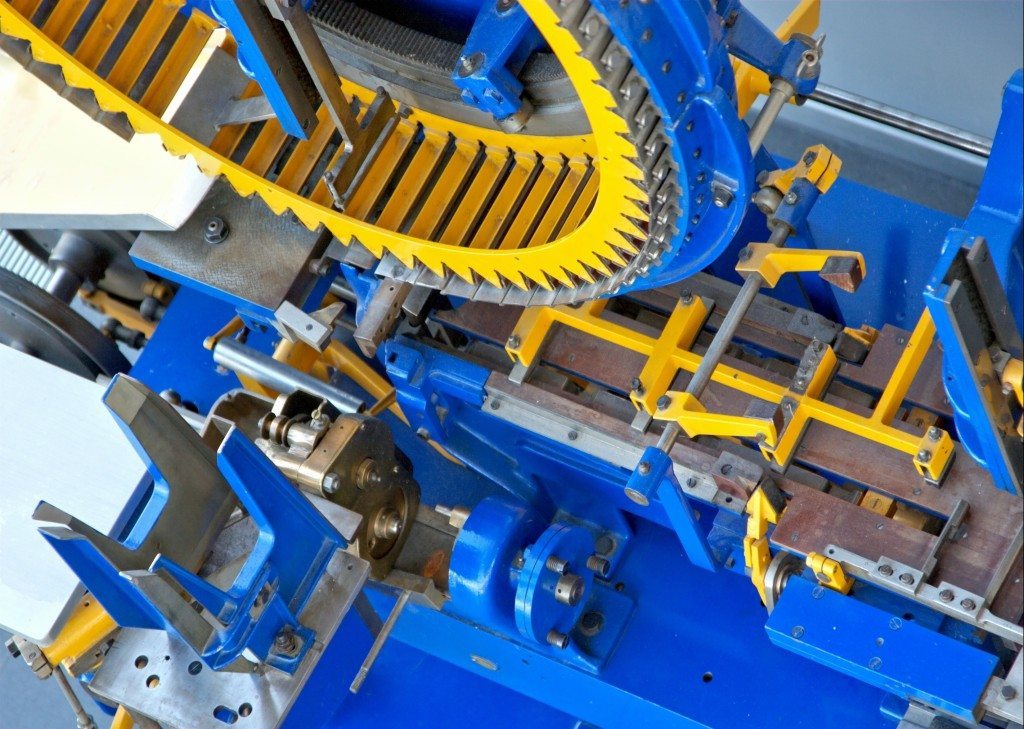
The field level is the lowest automation hierarchy level and is made up of field devices such as actuators and sensors. The field devices have a core task of transferring machines and processes data to the next level for monitoring and analysis. Actuators are used to control the process parameters. In most cases, this level is dubbed the arms and eyes of an automated industrial process. Real time process parameters such as level, flow, temperature, and pressure are converted into electrical signals by the field level sensors. Data collected from the sensors is transferred to the controller for further monitoring and analysis of the real time parameters. Sensors include; proximity sensors, flow meters, thermocouple, RTDs among others. Actuators include; pneumatic actuators, flow control valves, relays, solenoid valves, servo motors, and Dc motors among others.
The control level
The control level is made up of automation devices such as PLCs and CNC machines that derive ideal process parameters from the different sensors. Industrial automated controllers trigger the actuators as per the processed sensor signals, control techniques, or programs. PLCs (programmable logic controllers) are widely used as industrial controllers of choice because they can deliver automatic control functionalities as per sensors’ inputs. PLCs allow industrial automation operators to program control functions to execute automatic process operations. PLCs are made of different modules such as; digital I/O, communication modules, analog I/O and CPU.
Production control and supervising level
At this level, automatic monitoring systems and devices are used to facilitate the intervention and control of functions such as; setting of production targets, supervising different parameters, supervisory control and data acquisition (SCADA), setting machine start and stop periods, and Human Machine Interface (HMI).
At this level, a manufacturing execution system (MES) is an information system that connects, monitors and controls complex manufacturing systems and data flows on the factory floor. The main goal of an MES is to ensure effective execution of the manufacturing operations and improve production output.
Enterprise or information level
Often referred to as Enterprise Resource Planning (ERP), this is the top industrial automation hierarchy level that is tasked with management of the entire industrial automation system. Tasked executed at this level include; market and customer analysis, sales, orders, and production planning just to mention a few. Evidently, this level is geared towards supporting commercial industrial activities as opposed to technical industrial aspects. Note that, all industrial automation hierarchy levels comprise of industrial communication networks that transfer information from one hierarchy level to another. As such, they ensure continuous flow of information but the communication networks can vary from one hierarchy level to the other.
Summary
The industrial automation hierarchy takes on a pyramid form of communications where information gets aggregated as it moves from a low level (sensor level) to high level (Server or enterprise level) and there is a direct correlation between the levels of the hierarchy in that improved communications between levels of the hierarch lead to direct efficiency increases of the overall manufacturing systems. In fact, this is the basis of Industry 4.0 and Made in China 2025 initiatives.