Mechanics of Motion Control Systems
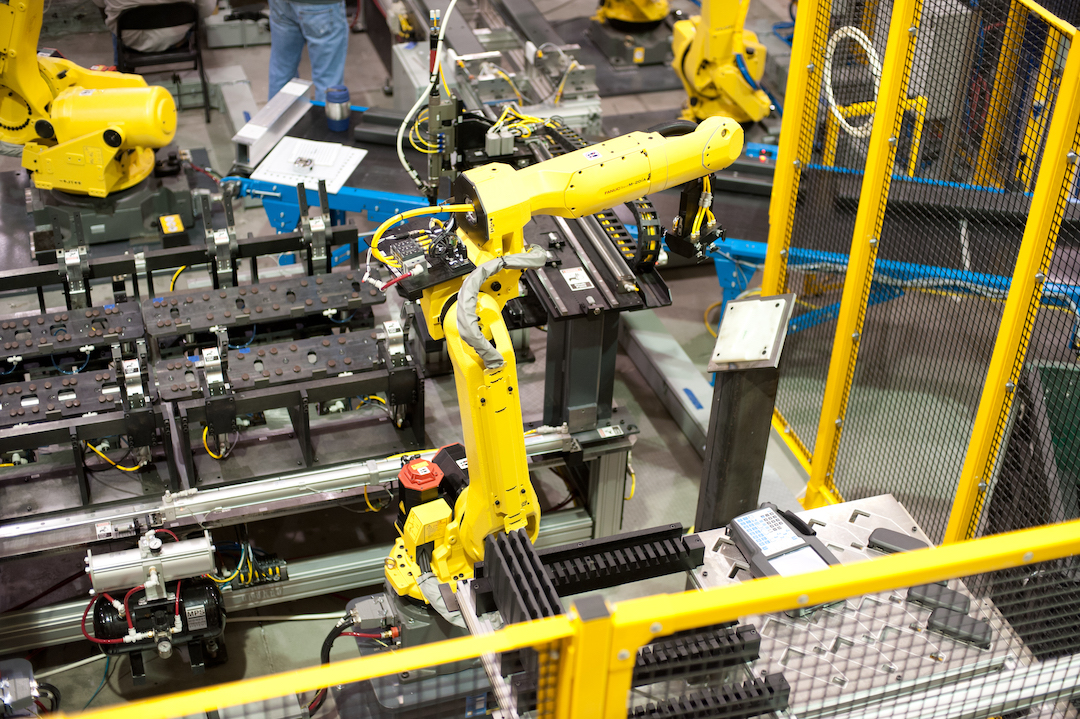
Mechanical actuators
Mechanical actuators main purpose is to offer a mode of converting the motion of a motor rotary into linear motion. Though some mechanical actuators have backlash, they all have finite axial and torsional stiffness levels that affect system frequency response features directly. Mechanical actuator options entails; ball screws, lead screws, rack and pinion, belt, chain or cable drives.
Linear bearings and linear guides
Linear bearings maintain a translating load that is constrained to a single freedom degree. If features technologies such as recirculating and non-recirculating rolling elements, profile shaped and round guides, hydrostatic, air and magnetic bearings as well as sliding type guides. Crucial linear bearings and guide attributes include; straightness, load capacity, smoothness, static friction, dynamic friction, rigidity, installation mounting surface preparation, and flatness.
Machine structure
Machine structure affects a motion control system in complex ways. Meaning that, a well-designed machine structure reduces the injection requirements of external disturbances through incorporating a compliant and highly damped barrier that isolates a motion control system from its surrounding environment while still maintaining a sufficiently damped and stiff structure without resonance problems. Note that, a highly static mass to reciprocating mass ratio bars motion controls systems from exciting structures they are attached to.
Other important components
Other motion control system mechanical components include; way covers that protect them against dirt and cable carriers for retaining moving cables, shock absorbers for dissipating energy when a crash occurs, and end stops for restricting travels. Note that, any movable mechanical component impact motion control system response by altering the resonance, stiffness, inertia, friction, and damping amounts.
Motion control software and systems are responsible for the motion path planning computational requirements, sequence execution, and servo loop closure. As such, a motion control software dedicated computer is programmed to execute predetermined tasks. However, motion control system designer must consider unique application requirements and mechanical components required.